I'm redoing electronics on a Grady 307. First time doing work like this. Was going to replace the old Airmar B60 transducer with a thru hull B175HW. Was thinking the 60 would be easy to get out since the hole needed for the B175 is larger than 60, but I am terrified to cut a hold that large in the boat.
Below are pics of the bilge with a cutout of how large the B175 with the nut on would be. Looks a little tight. I'm assuming that wall to the left is a stringer. Any reason to avoid cutting a hole close to that? Is there anything else I could screw up when cutting a hole in bilge area? Anything structural I could ruin?
Also wondering which angle most use for the transducer on a 307. The B60 on the boat now is a 12 degree, but the hull is more like 20 degrees.
This forum has been great so far. Wondering what your thoughts are and if I should move forward with this myself or bring in the professionals?
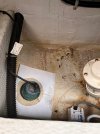
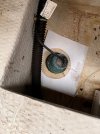
Below are pics of the bilge with a cutout of how large the B175 with the nut on would be. Looks a little tight. I'm assuming that wall to the left is a stringer. Any reason to avoid cutting a hole close to that? Is there anything else I could screw up when cutting a hole in bilge area? Anything structural I could ruin?
Also wondering which angle most use for the transducer on a 307. The B60 on the boat now is a 12 degree, but the hull is more like 20 degrees.
This forum has been great so far. Wondering what your thoughts are and if I should move forward with this myself or bring in the professionals?
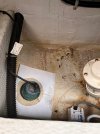
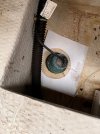