Your biggest challenge to start is an industrial sewing machine, preferably a walking foot model. As far as other tools,a pneumatic stapler. I also have an electric one but it isn't nearly as powerful as the pneumatic ( you need an air compressor of course) For supplies you have to decide on a foam choice unless you can reuse the old foam. I suspect that when you unwrap the old ones, you may be shocked at the mold in the foam.
If your bolsters have wrap around ends, unless you have sewing experience, you may want to reconsider doing it yourself.
I did mine to be an exact match to the original, including piping (welting) on end caps and backs, drainage material on the underside (
Phifertex ), Pleated vinyl, matching plain vinyl and premade welting (all Seaquest). I used Fastdry foam, water and glue run right through it. I got the staples online although some posted that they found monel in a retail store. I didn't. Gromets and punch for grommets. (cheap kits available at box stores.
I hope you can reuse your backings. Those are a pin to replicate.
For a somewhat novice sewer, the job was long and tedious. Just removing the old staples was miserable. I also ripped all the sewn seams, marked the pieces and used them as patterns for the new materials. In my case, the inside corners of the wrap around bolster were made from several pieces of plain vinyl. Making those is a lot more work than just making a corner miter with the pleated material. The pieced approach does look better though.
I can't tell you where to order the materials, many of the online stores I used are gone.
Here are a couple of pics showing the old parts disassembled
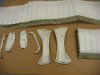
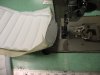
.