- Joined
- Sep 11, 2020
- Messages
- 92
- Reaction score
- 46
- Points
- 18
- Location
- Orange County, CA
- Model
- Gulfstream
I just installed a new Airmar B175HW through hull transducer in my 232 Gulfstream. When I bought the boat, it had an abandoned through hull installed. This new B175HW is much larger - 3 3/4" diameter. The good news is that the hole saw fit over the old transducer, so I did not have to wrestle with trying to uninstall it. I just cut it out as you can see in the pictures:
Once I got the hole cut, I sanded the bottom paint from the mating surface of the hull, taped over the transducer, cut the tape to leave a clean barrier, and cleaned it with Xylene. I also cleaned the inside of the hull where the rubber gasket will seal. Taking the time to tape well really makes clean-up a breeze.
I test fit the transducer a few times to ensure it is seating properly. I then fed the wire through the hole and applied a thick bead of West Marine 8200 sealant around the flange of the transducer. I inserted the transducer into the hole and taped it in place from the outside. Ensure that you see plenty of sealant squeeze out from all around the transducer flange.
Make sure that the arrow on the transducer is pointing directly to the keel (center line of boat). This one is a 20* tilted element that need to be facing the right way so it fires straight down.
I was then able to add more sealant around the transducer on the inside prior to installing the rubber gasket, the plastic spacer, and the large nut.
I used a couple pair of large channel lock pliers to hold the transducer from spinning while I securely tightened the large nut. I snugged it down as much as I could, then tightened the two locking screws on the nut.
Then clean up: This is where time spent taping good pays off. I just pealed the tape on the bottom and all the dripping sealant came off with it. A quick smoothing of a bead of sealant around the flange and it is done.
Lastly, I fed the cable through the hull conduit and up behind the instrument panel.
I need to give the adhesive sealant a few days to fully cure before I try it out. I hope to put it in the water this weekend.
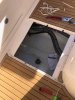
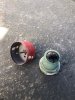
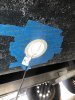

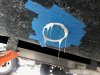
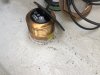
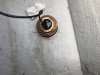
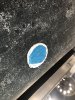
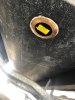

Once I got the hole cut, I sanded the bottom paint from the mating surface of the hull, taped over the transducer, cut the tape to leave a clean barrier, and cleaned it with Xylene. I also cleaned the inside of the hull where the rubber gasket will seal. Taking the time to tape well really makes clean-up a breeze.
I test fit the transducer a few times to ensure it is seating properly. I then fed the wire through the hole and applied a thick bead of West Marine 8200 sealant around the flange of the transducer. I inserted the transducer into the hole and taped it in place from the outside. Ensure that you see plenty of sealant squeeze out from all around the transducer flange.
Make sure that the arrow on the transducer is pointing directly to the keel (center line of boat). This one is a 20* tilted element that need to be facing the right way so it fires straight down.
I was then able to add more sealant around the transducer on the inside prior to installing the rubber gasket, the plastic spacer, and the large nut.
I used a couple pair of large channel lock pliers to hold the transducer from spinning while I securely tightened the large nut. I snugged it down as much as I could, then tightened the two locking screws on the nut.
Then clean up: This is where time spent taping good pays off. I just pealed the tape on the bottom and all the dripping sealant came off with it. A quick smoothing of a bead of sealant around the flange and it is done.
Lastly, I fed the cable through the hull conduit and up behind the instrument panel.
I need to give the adhesive sealant a few days to fully cure before I try it out. I hope to put it in the water this weekend.
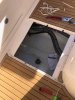
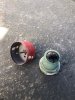
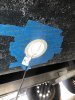

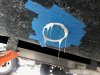
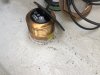
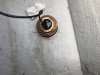
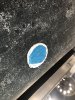
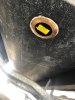
